T1 Test to check molten metal flow and trial production
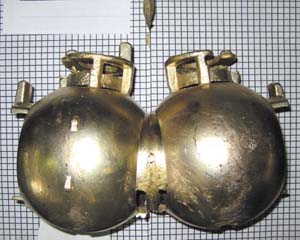
Metalmold temperature approximately 100°C
Temperatureduring pouring about 1015°C
Molten metal flow is good
Molten metal is filled all the way up to up-hill part for degassing.
Whenthe product was made with a plan with fast molten metal flow supplied toproduct parts, overall run was sufficient.
Metalmold plan for Permanent mold casting has a marked influence on molten metal flow.
Adefect was found in trial production caused by shrinkage in the part sandwichedby the core, which is the part that solidifies last.
We believe the defect can be resolved by using adifferent gate thickness and position.
Thevarying components due to Zn depletion in molten metal appeared to causechanges in the flow of molten metal.
T2 Teeter mold test
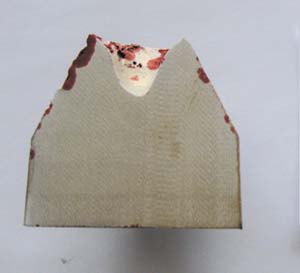
Result: Good It can be used for Permanent mold casting
Internalshrinkage showed a smooth surface.
Thedeepest part of shrinkage did not contain any rough textured surface stainedred on color check.(It is good)
A plan that considers the possibility of relatively large external overall shrinkageand relatively large and shallow internal shrinkageis required.
Metalmold casting conditions may not be suitable.
A temperature range must be used that is suitable for Permanent mold casting.
T3 Confirmation of mechanical properties
Tensilestrength: 357 N/mm2 Degreeof elongation: 30%
Standardsof common brass material and bronze were met sufficiently.
T4 Analysis and confirmation of molten metal components
Cu | Sn | Pb | Zn | Fe | Bi | Se | Other | Cd | ||
---|---|---|---|---|---|---|---|---|---|---|
1. | Standard value | 57.5-60.5 | 1.0Max | 0.01Max | REM | 0.4Max | – | – | 0.15-0.55 | |
2. | Purchased materials | 58.8 | 0.2 | 0 | 40.78 | 0.01 | – | – | 0.21 | 6ppm |
3. | Before melting | 59 | 0.2 | 0.003 | 38.8 | 0.005 | 2.17 | 0.033 | 0.17 | 6ppm |
4. | At the time of test production | 59.3 | 0.29 | 0.004 | 37.52 | 0.007 | 1.96 | 0.033 | 0.2 | 6ppm |
Attentionis required as Zn tends to be depleted and the value of Cu tends to increase.
T5 Confirming processability
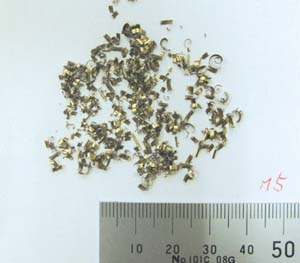
Itappeared to be viscous.
Chipsare small but larger than those of common brass.
Processabilityis good.
T6 Evaluation of pressure resistance of trial production
Result
In thetrue trial production, the degree of leakage was lower, but we were unable toimprove leakage from the part sandwiched by the core.Metalmold plan and casting condition have large effects on pressure resistance. Wewill continue to examine its properties.
Preliminary trial production
Leakage was observed in all products in preliminarytrial production.Leakagewas observed at the part sandwiched by core sand that solidifies last.Therewas no leakage at the part in direct contact with the metal mold.
True trial production
In thetrue trial production where plan and product thickness were changed, the degreeof leakage was improved but the plan is not perfect.
Results and evaluation
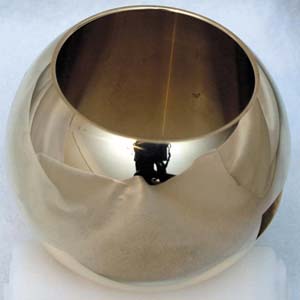
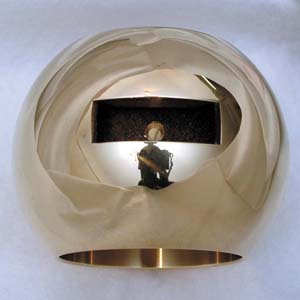
If thecomponents of molten metal are sufficiently managed, metal mold castability byPermanent mold casting is good.
Thismaterial was not developed as a Permanent mold casting material.
It canbe used for sealed type low-pressure Permanent mold casting.
Utilizationin low-pressure Permanent mold casting may be easier than in gravity metal moldcasting method.
However,optimal balance of molten metal components and Permanent mold casting conditions,such as pouring temperature and metal mold temperature, must be investigated.
Importanceof the Permanent mold casting plan is high, and it is necessary to change thecharacteristics of the plan from that used for common lead-containing brass