T1 Test to check molten metal flow and trial production
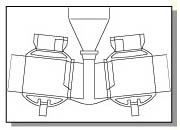
Gravity Permanent mold casting method was used for trial production of Permanent mold casting, and molten metal flow was checked.
Through both preliminary and true trial production of Permanent mold casting, the molten metal flowability of each material was examined.
A Permanent mold casting experiment was conducted using a common Permanent mold casting metal mold plan for materials M1 to M8.
T2 Teeter mold test
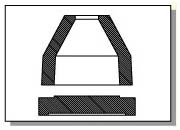
Test to observe and confirm the shrinkage of materials during solidification.
Differences in the solidification process in the final solidified spot were determined from the differences in shrinkage cavity morphology, and shrinkage of the material was determined.
Size of test specimen:Diameter of bottom surface 68 mm, height 72 mm
T3 Confirmation of mechanical properties
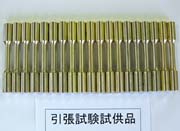
Thetensile strength and degree of elongation for test specimens of each materialcollected through Permanent mold casting were confirmed using JIS Z 2241.
・Tensile specimen collection method:Size B sample material was used based on JIS standard brass castings.
・Test specimen:The test specimen was based on size 4 test specimen of JIS Z 2201.
Reference standard value
・CAC203 (JIS standard) tensile strength ≥ 245 N/mm2 and, degree of elongation ≥ 20%
・CAC406(JIS standard) tensile strength ≥ 195N/mm2and, degree of elongation ≥ 15%
T4 Analysis and confirmation of molten metal components
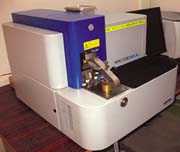
Asolid metal emission spectrophotometer (SPECTRO A.I.) was used to examine thecomponents of each molten metal during testing to determine the Pb and Cdcontents as well as the amount mixed in when melted.
1.Specification at the time of purchase (manufacturerdefault value on the mill sheet at the time of purchase)
2.Millsheet data at the time of purchase (values with no Cd measurement value weremeasured by our company)
3.Measuredvalues of purchased material before melting using our company’s equipment (thevalues do not necessarily match those provided by the manufacturer due to errorof measurement and calibration method)
4.Analysisof components of molten metal at trial product casting
T5 Confirming processability
Thecharacteristics of each material were better understood by checking thecondition of chips occurring during cutting in trial production. (Eachmaterial was cut with tools and conditions used for common brass material anddifferences were noted.)
T6 Evaluation of pressure resistance of trial production
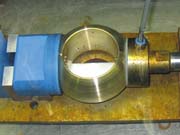
Trialproduct after cutting was placed into a water immersion-type compressionleakage tester to observe leakage condition(Airpressure test at 0.4 MPa)